گندله چیست؟ معرفی انواع گندله و تفاوت آن با سایر مواد اولیه
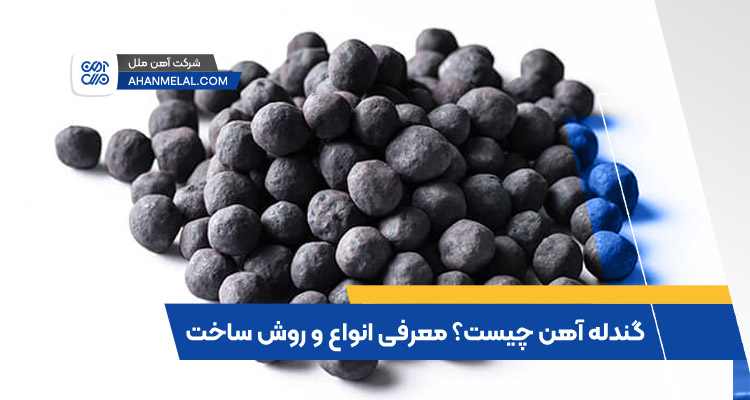
گندله، همان گلولههای کوچک تشکیلشده از سنگآهن نرم و مواد دیگری است که در ابتدا بهصورت خام بوده، اما طی چند مرحله، پخته و سخت می شود. از گندله آهن در کوره بلند و کوره های احیاء مستقیم برای تولید شمش فولادی استفاده می شود. انواع گندله با توجه به سایز گلوله ها به سه دسته ریز، معمولی و درشت تقسیم می شوند. آشنایی با کاربرد انواع گندله، روش چهار مرحلهای تولید گندله و همچنین تفاوت گندله با سایر مواد اولیه در زنجیره تولید فولاد (مانند کنسانتره، آهن اسفنجی، بریکت و کلوخه) برای فعالان این صنعت امری ضروری است و ما را بر آن داشت تا به طول کامل و با بیانی ساده به معرفی این محصول بپردازیم.

نسخه صوتی مقاله گندله آهن چیست؟
آهن ملل | ویژگی های محصول | |
---|---|---|
۱ | نام محصول | گندله آهن (Iron ore pellets) |
۲ | انواع | ۱- گندله ریز با قطر ۳ تا ۸ mm ۲- گندله معمولی با قطر ۱۰ تا ۱۵ mm ۳- گندله درشت با قطر ۲۰ تا ۳۰ mm |
۳ | مواد اولیه ساخت گندله | کنسانتره آهن + پودر بنتونیت + سود سوزآور |
۴ | کابرد | صنعت فولاد (تولید آهن اسفنجی و شمش فولادی) |
گندله چیست؟
گندله (با تلفظ: گُندِلِه) یکی از مواد اولیه و مهم در تولید شمش فولادی و همچنین مقاطع فولادی است. این محصول، در واقع گلوله های کوچک آهن است که با استفاده از سنگ آهن و دیگر مواد افزودنی ساخته می شود.
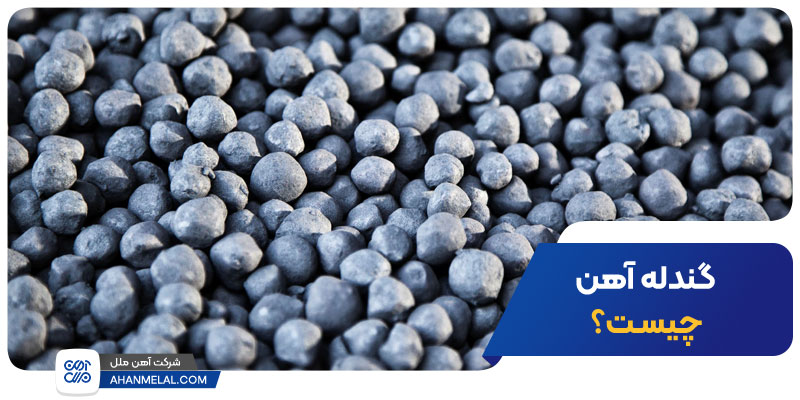
- رنگ گندله، مشابه رنگ آهن و خاکستری رنگ است.
- «گندله» به انگلیسی Pellet و «گندله سنگ آهن» به انگلیسی Iron ore pellets نامیده می شود.
اهمیت استفاده از گندله در تولید شمش و صنعت فولاد به قدری است که می توان گفت کیفیت نهایی محصولات فولادی به کیفیت گندله و کیفیت شمش وابسته است. توصیه می کنیم با روش تولید شمش فولادی و جایگاه آن در صنعت فولاد در مقاله زیر نیز آشنا شوید.
# حتما بخوانید
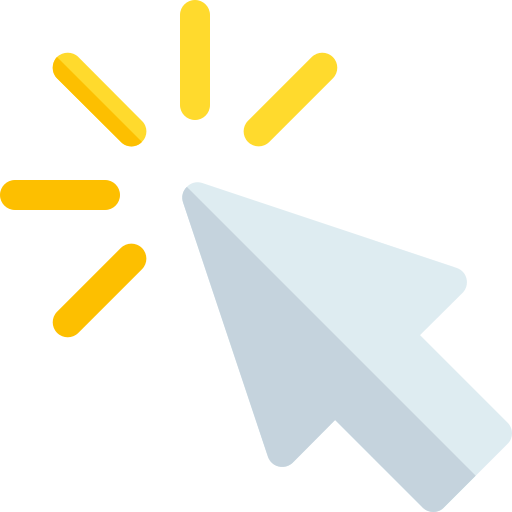
معرفی انواع گندله
گندله ها را از نظر ابعاد می توان به سه دسته تقسیم بندی کرد:
- گندله با قطر ۳ تا ۸ میلی متر: گندله های ریز برای کلوخه سازی و فرآیند هیدرومتالورژی استفاده می شوند.
- گندله با قطر ۱۰ تا ۱۵ میلی متر: این سایز گندله معمولترین گندله در صنعت است که در کوره بلند و واحدهای احیای مستقیم استفاده می شود.
- گندله با قطر ۲۰ تا ۳۰ میلی متر: این نوع گندله در فولادسازی و به عنوان مواد خام برای تولید سیمان کاربرد دارد.
نوع دیگر گندله که می توان آن را از گندله عادی متمایز کرد، گندله اسفنجی است.
آشنایی با انواع گندله، اهمیت زیادی در انتخاب و استفاده از آن ها دارد؛ زیرا وقتی ابعاد گندله متفاوت باشد، نیروی لازم برای خرد شدن آن ها نیز متفاوت خواهد بود. به طور مثال، استحکام گندله هایی با قطر ۱۴ میلی متر حدود ۲۰ تا ۵۰ نیوتن است.
گندله چگونه تولید می شود؟
محصول گندله در واحد گندله سازی (Pelletizing plant) و با استفاده از پودر کنسانتره سنگ آهن جهت مصرف در صنایع فولاد تولید می شود. نحوه گندله سازی، معمولا شامل چهار مرحله آماده سازی مواد خام، مخلوط کردن، گلوله سازی و سخت شدن است. مراحل گندله سازی را در ادامه، بیشتر بررسی می کنیم.
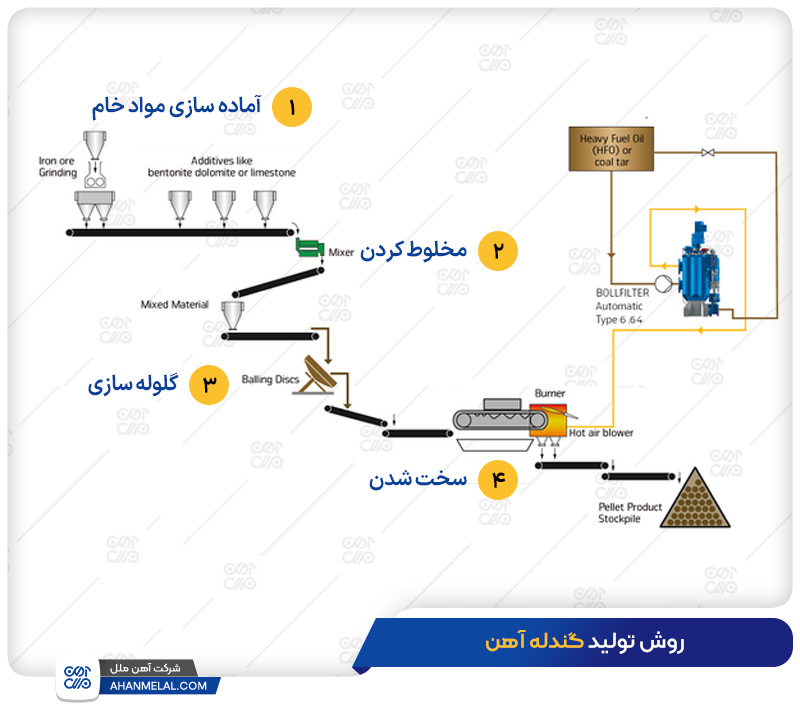
۱- کنسانتره آهن زبره با خلوص ۶۷.۵ درصد در آسیاب های واحد گندله سازی به صورت پودر درمی آید.
۲- بعد از این که پودر با دانهبندی مناسب آماده شد، در بخش میکسرها با کنسانتره آهن ریزدانه، چسب (پودر بنتونیت) و سود سوزآور به دیسک های دوار ارسال می شود.
۳- در دیسک دوار، مخلوط پودر کنسانتره آهن به صورت گلوله هایی معمولا به اندازه ۸ تا ۱۶ میلی متر و یا بیشتر در می آید.
۴- در نهایت، پس از خشک شدن (Rotary Kiln) و پیشگرم (Chain great) در کوره ای افقی با حرارت حدود ۱۲۵۰ تا ۱۳۰۰ درجه سانتیگراد پخته و سخت می شود. پس از سردشدن (Annular Cooler) نیز به واحدهای احیاء مستقیم یا انباشت و برداشت انتقال می یابد.
این روش تولید گندله به «آلیس چالمرز» معروف می باشد. یکی از مهم ترین ویژگی های این روش، کیفیت بالای گندله های تولیدی از نظر پخت سطحی و عمقی یکنواخت است. همین مسئله باعث افزایش استحکام فشاری سرد و بهبود سایر خواص مکانیکی گندله می شود و در زمان حمل و نقل نیز هدر رفت گندله نرمه را به حداقل می رساند.
استانداردهای تولید گندله آهن چیست؟
استاندارد ملی ایران در تولید گندله سنگ آهن در چندین بخش برای تعیین شاخص های تامبلر و سایش، تعیین استحکام خُردشوندگی و همچنین روش های آزمون، توسط «کمیته ملی استاندارد مهندسی ساختمان و مصالح و فرآورده های ساختمانی» تدوین شده است که می توانید در ادامه جزئیات آن را مشاهده کنید.
استانداردهای ملی ایران برای تولید گندله آهن (Iron ore pellets) | ||
شماره استاندارد | عنوان استاندارد | سال تدوین |
۴۹۷۷ | سنگدانهها– دانهبندی سنگدانه های ریز و درشت– روش آزمون | ۱۴۰۱ |
۱۲۸۰۹ | کانه های آهن – مواد اولیه برای کوره بلند و احیای مستقیم -تعیین استحکام خرد شوندگی | ۱۳۹۵ |
۱۲۶۷ | کانه های آهن – مواد اولیه برای کوره بلند و احیای مستقیم -تعیین شاخص های تامبلر و سایش | ۱۳۹۵ |
کاربرد گندله چیست؟
کاربرد اصلی گندله به عنوان ماده اولیه در تولید فولاد است. این محصول در زنجیره تولید فولاد، در کوره های احیاء مستقیم و کوره بلند کاربرد دارد. به طور کلی، موارد مصرف گندله را می توان به دو دسته زیر تقسیم بندی کرد:
- برای تولید آهن اسفنجی به روش احیاء مستقیم
- تأمین نیاز صنایع مختلف به مواد اولیه
جایگاه گندله در زنجیره تولید مقاطع فولادی
گندله سازی، یکی از قسمت های مهم در تولید شمش فولادی و همچنین تولید محصولات فولادی است.
زنجیره کامل تولید شمش و مقاطع فولادی به این ترتیب است:
واحد کنسانتره
واحد گندله سازی
واحد تولید آهن اسفنجی
واحد ذوب و فولاد
و کارخانه نورد برای تولید مقاطع فولادی
شروع چرخه تولید به این صورت است: پودر سنگ آهنی که از معادن استخراج شده، به واحد انباشت و برداشت کارخانه فولادسازی منتقل می شود. (مراحل تولید سنگ آهن را می توانید در همه چیز در مورد سنگ آهن بخوانید) سپس این پودر سنگ در واحد گندله سازی طی چند مرحله و ترکیب با مواد دیگر به گندله تبدیل می شود. در ادامه نیز گندله در واحد احیاء مستقیم به آهن اسنفجی تبدیل می گردد و مراحل به همین صورت ادامه پیدا می کند تا در کارخانه نورد انواع محصولات فولادی مانند ورق آهن، میلگرد، تیرآهن و … تولید شود.
مزایای استفاده از گندله
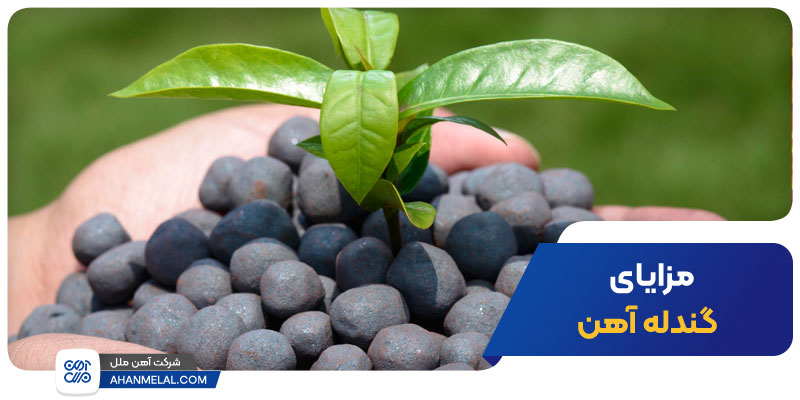
استفاده از گندله سنگ آهن در صنایع فولادی مزایای زیر را به همراه دارد:
- کاهش مصرف انرژی
- افزایش کارایی کوره های قوس الکتریکی و کوره های بلند
- کاهش آلودگی محیط زیست
- سهولت در انبار کردن
- تضمین تولید فولاد با کیفیت بالا
اصطلاحاتی که باید در مورد گندله بدانید
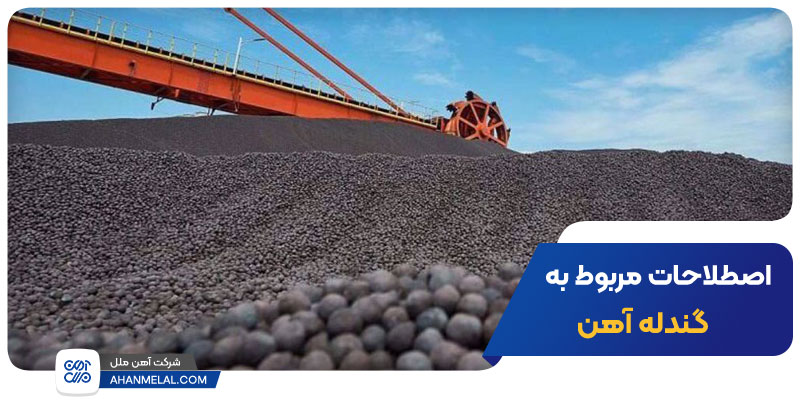
کاربرد فراوان گندله فولاد در صنایع مختلف باعث شده این محصول اهمیت زیادی برای فعالان صنایع مختلف و به خصوص صنعت فولاد داشته باشد. از این رو به بررسی اصطلاحات رایج مورد استفاده برای گندله می پردازیم.
۱- CCS گندله چیست؟
CCS مخفف Cold Crushing Strength به معنای استحکام فشاری سرد است.
CCS گندله پارامتر نشان دهنده کیفیت گندله است که با استفاده از دستگاهی به نام پرس هیدرولیک تعیین می شود. برای این منظور، حداکثر فشاری که گندله می تواند تحمل کند و خرد نشود، اندازه گیری شده و به عنوان CCS گندله اعلام می شود. هر چه CCS گندله بالاتر باشد، قدرت و مقاومت آن نیز بیشتر است.
۲- تخلخل گندله چیست؟
یکی دیگر از پارامترهای کنترل کیفیت گندله، تخلخل گندله است که نتیجه حذف یکنواخت آب و تبخیر آن می باشد. منظور از تخلخل، حجم حفره های داخل گندله به حجم کل گندله خام است. این مقدار در بهترین حالت ۲۰ تا ۳۰ درصد می باشد.
۳- چگالی گندله چیست؟
بین تخلخل و چگالی گندله رابطه معکوس وجود دارد. بنا بر این با افزایش تخلخل، چگالی گندله کاهش می یابد.
۴- نرمه گندله چیست؟
به پودری که کف کوره های گندله سازی باقی می ماند، نرمه گندله آهن می گویند. نرمه گندله سنگ آهن، دانه های ریز (زیر ۶ میلی متر) گندله است که کاربرد بسیاری در رنجیره فولادسازی و دیگر صنایع، مانند تولید لنت ترمز خودرو دارد. رنگ آن نیز معمولا قهوه ای و در برخی موارد، مشکی و کرمی است.
از مزایای نرمه گندله، قابلیت بازیافت آن است؛ به این صورت که می توان با آسیاب کردن، آن را به کنسانتره آهن تبدیل کرد و به خط گندله سازی برگرداند. این کار تا حدود زیادی به کاهش هدررفت در رنجیره تولید فولاد و محصولات خام آهنی کمک می کند.
چه عواملی در قیمت گندله آهن تاثیر دارد؟
از مهم ترین پارامترهای تاثیرگذار بر قیمت گندله آهن، میزان شاخص اکسید آهن (FeO) در محصول نهایی است؛ به این صورت که هر چه مقدار FeO در محدوده بهینه باشد، کیفیت و قیمت گندله بالاتر است. (مقدار ایده آل اکسید آهن (FeO) بین ۰.۴ تا ۰.۶ است.)
طبق تحقیقات آکادمیک و آزمایشات انجام شده، چهل و پنج عامل بر شاخص FeO در تولید گندله تاثیرگذار است که از بین همه این موارد، دو عامل اکسید منیزیم و جریان هوایِ فن ورودی دستگاه سفت کننده، بیشترین تأثیر را روی FeO گندله های آهن دارد. نتایج این پژوهش با استفاده از تکنیک داده کاوی و در کارخانه گندله سازی گل گهر سیرجان انجام شده است.
کارخانه های تولیدکننده گندله در ایران
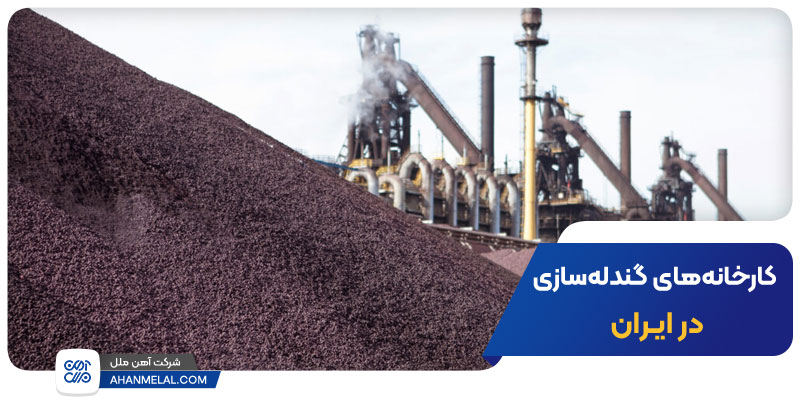
کارخانه های گندله سازی سنگ آهن به دلیل فناوری پیشرفته تولید و استفاده از فرآیند تولید خودکار، نیازهای بسیاری از صنایع را برآورده می کنند. از جمله مهم ترین کارخانه های گندله سازی در ایران می توان به موارد زیر اشاره کرد:
لیست گندله سازی های ایران:
- کارخانه فولاد مبارکه اصفهان
- شرکت مجتمع فولاد اردکان
- شرکت معدنی و صنعتی چادرملو
- مجتمع گندله سازی بهاباد
- شرکت اپال پارسیان سنگان
- کارخانه گندله سازی خرامه
- مجتمع تولید گندله سنگ آهن مادکوش
- شرکت معدنی و صنعتی گل گهر
- مجتمع فولاد بافق
- گندله سازی صبا نور – کارخانه کنسانتره صبا نور
- شرکت صبا امید غرب خاورمیانه
- شرکت توسعه معدنی و صنعتی صبانور (گندله سازی همدان)
- کارخانه فولاد زرند ایرانیان
- شرکت فولاد خراسان (گندله نیشابور)
- گندله سازی غدیر
تفاوت گندله و کنسانتره
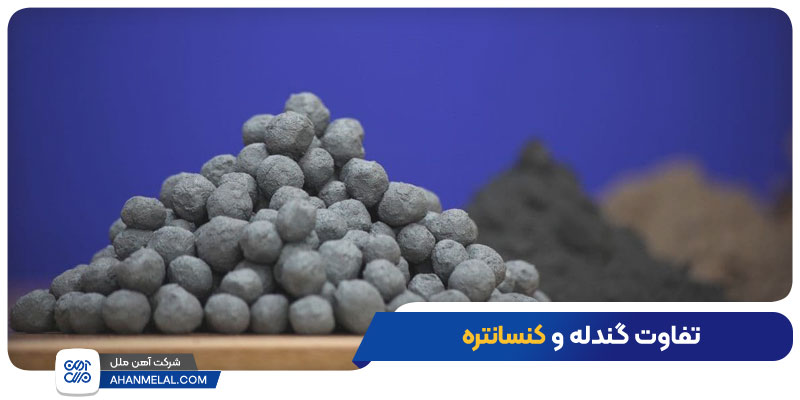
با دانستن این که «کنسانتره سنگ آهن، مواد اولیه برای تولید گندله است»، فرق گندله و کنسانتره مشخص می شود.
روش کار به این صورت است ابتدا کنسانتره سنگ آهن طی مراحل زیر تولید می شود، سپس با استفاده از کنسانتره، گندله تولید می شود.
سنگ آهن استخراج شده از معدن، خرد و آسیاب می شود. سپس مواد با ارزش از ذرات زائد جدا شده و در مرحله آخر، جداکردن و خشک کردن آبِ درون ذرات انجام می شود. در نهایت، کنسانتره سنگ آهن که به شکل پودری سیاه رنگ است و رطوبت کمتر از ۱۰ درصد دارد به دست می آید.
از آنجا که کنسانتر به طور مستقیم در واحد ذوب و احیا قابل استفاده نیست، آن را به گندله تبدیل کرده و در واحد ذوب و احیا استفاده می کنند.
تفاوت گندله و آهن اسفنجی
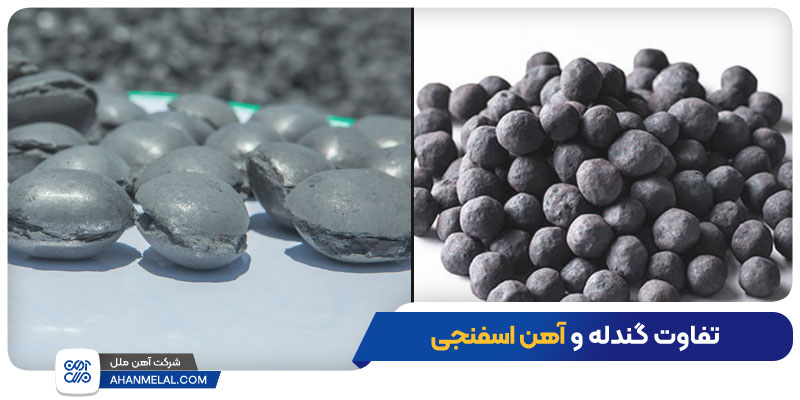
فرق گندله و آهن اسفنجی در زنجیره تولید محصول است. در واقع، به گندلهی احیا شده، آهن اسفنجی می گویند. مراحل تبدیل گندله به آهن اسفنجی نیز به این صورت است:
در زنجیره تولید شمش فولادی، وظیفه واحد احیاء، تبدیل گندله اکسیدی به آهن اسفنجی است. به این صورت که گندله پخته شده وارد کوره احیاء با دمای ۸۰۰ درجه سانتیگراد شده و گاز احیاءکننده نیز با دمای حدود ۹۰۰ درجه سانتیگراد حرارت به داخل کوره دمیده میشود. پس از چند مرحله، گندله احیاشده (آهن اسفنجی) از کوره ها خارج و پس از ذخیره سازی در سیلوهای مخصوص، بر اساس نیاز ناحیه فولادسازی به این واحد ارسال میگردد. توصیه می کنیم جزئیات بیشتر در مورد آهن اسفنجی را در مقاله آهن اسفنجی چیست بخوانید.
تفاوت گندله با آهن اسفنجی در قیمت نیز یکی دیگر از موارد قابل بررسی است. همانطور که گفتیم آهن اسفنجی با استفاده از گندله تولید می شود، در نتیجه قیمت آهن اسفنجی به صورت مستقیم متاثر از قیمت گندله بوده و همواره بالاتر از گندله است. قیمت آهن اسفنجی را می توانید در لینک زیر مشاهده کنید.
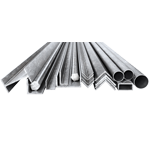
مشاهده قیمت و خرید انواع مواد اولیه برای تولید شمش فولادی
آهن ملل؛ مرکز فروش آهن اسفنجی به صورت آنلاین و حضوری
قیمت آهن اسفنجیتفاوت گندله و بریکت
بریکت، نوعی آهن اسفنجی فشرده است. به عبارت دیگر، محصولی است که بعد از تولید گندله و آهن اسفنجی تولید می شود.
برای تولید بریکت، ریزدانه های آهن اسفنجی (که با استفاده از گندله ساخته می شوند) به واحد بریکت سازی ارسال می شوند. در این مرحله با عملیات فشرده سازی، بریکت آهن اسفنجی تولید می شود. بیشترین مزیت بریکت سهولت در حمل و نقل، نگهداری و ذخیره سازی آن است.
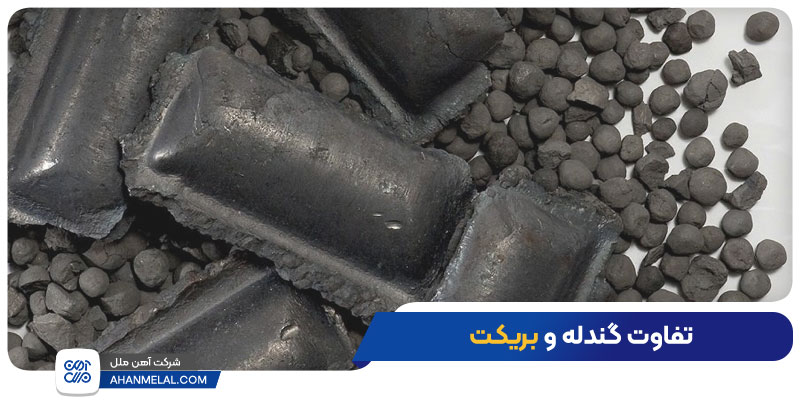
تفاوت کلوخه و گندله
گندله و کلوخه هر دو از مواد اولیه در فرآیند فولادسازی هستند و از سنگ آهن به دست می آیند، اما تفاوت های زیادی با یکدیگر دارند. در واقع، گندله و کلوخه، هردو برای استفاده در کوره مناسب هستند؛ اما می توان آن ها را از نظر مواد اولیه و نحوه تولید، اینگونه مقایسه کرد:
کلوخه آهن از سوزاندن مخلوطی از نرمه آهن، کمکذوبها و مواد بازیافت شده ساخته میشود؛ اما برای ساخت گندله، برخلاف کلوخه، از مواد بازیافتی کارخانجات استفاده نمی شود.
از نظر روش ساخت نیز گندله طی چهار مرحله آماده سازی مواد خام، مخلوط کردن، گلوله سازی و سخت شدن تولید می شود؛ اما کلوخه با فرایند آگلومراسیون* حرارتی تولید می شود و از نظر مقاومت دمایی، ویژگیهای مکانیکی و شیمیایی و همچنین ابعاد، برای استفاده در کوره مناسب است.
* آگلومراسیون، شامل مراحل آمادهسازی مواد، پخت و سردکردن می باشد.
سخن آخر
گندله از جمله مواد اولیهای است که در تولید فولاد و محصولات فولادی کاربرد دارد. این محصول به شکل گلولههای قهوه ای یا خاکستری رنگ است که از مخلوط کنسانتره سنگ آهن و دیگر مواد افزودنی تولید می شود. استفاده از گندله در صنعت فولاد باعث کاهش مصرف انرژی، افزایش کارایی کوره ها، کاهش آلودگی محیط زیست و سهولت در انبار کردن می شود.
سوالات رایج
گندله چیست و انواع آن کدام است؟
گندله، یکی از مواد اولیه برای تولید شمش فولادی است. شکل ظاهری گندله به صورت گلوله های کوچک است که از نرمه سنگ آهن و سایر مواد افزودنی ساخه می شود. انواع گندله با توجه به سایز گلوله ها به سه دسته ریز، معمولی و درشت تقسیم می شوند.
گندله سازی چیست؟
واحد گندله سازی یا Pelletizing plant قسمتی از زنجیره تولید فولاد است که در آن با استفاده از پودر کنسانتره سنگ آهن، گندله تولید می شود. در واحد گندله سازی، معمولا ۴ مرحله آماده کردن مواد خام، مخلوط کردن مواد، گلوله سازی و سخت شدن انجام می شود.
گندله برای چیست؟
گندله سازی به منظور تولید شمش فولادی انجام می شود. در واقع برای استفاده از سنگ آهن در تولید شمش باید ابتدا آن را به گندله تبدیل کرد.
اولین و دومین واحد گندله سازی کشور در فولاد خوزستان نصب و به بهره برداری رسیده است سایر گندله سازی های کشور توسط پرسنل فولاد خوزستان راه اندازی شده اند ولی اسمی از این شرکت برده نشده!!!!!!
سلام و وقت بخیر
ممنون از اطلاعاتی که در اختیارمون گذاشتید. حتما بعد از بررسی مقاله آپدیت می شود.