مواد اولیه فولاد سازی و روش های تولید فولاد
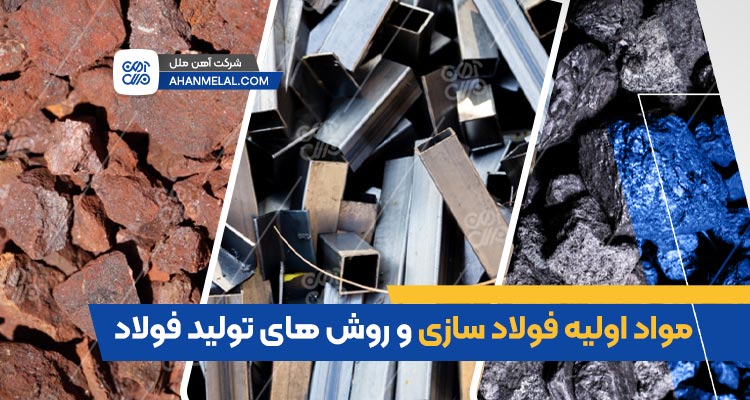
بعضی مواد اولیه فولاد سازی از مصالح ساختمانی است. باورتان نمی شود ولی همین سنگ آهک که برای ساخت گچ به کار می رود برای فولاد سازی هم استفاده می شود. مثلا برای تولید هر ۱ تُن فولاد خام، ۲۷۰ کیلوگرم سنگ آهک مصرف می شود. البته این ۲۷۰ کیلوگرم در روش های تولید فولاد متفاوت است. برای همین در این مقاله می خواهیم روش های تولید فولاد را هم توضیح دهیم.

نسخه صوتی مقاله مواد اولیه فولاد سازی و روش های تولید فولاد
مواد اولیه فولاد چیست؟
طبق تعریف انجمن جهانی فولاد، مواد اولیه فولاد شامل سنگ آهن، زغال سنگ، سنگ آهک، قراضه آهن و گُندله سنگ آهن می شود. البته این مواد در روش تولید فولاد با کوره بلند (BF) به کار می رود. در روش تولید فولاد با کوره قوس الکتریکی (EAF) از آهن اسفنجی استفاده می شود. این دو روش را در بخش های بعدی با جزئیات بیشتر بررسی می کنیم. برویم مواد اولیه فولاد را با هم بررسی کنیم.
۱- سنگ آهن، مهمترین ماده اولیه فولاد
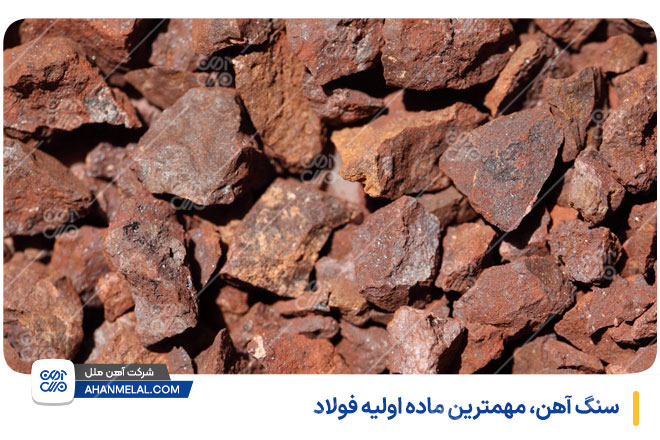
سنگ آهن از مواد اولیه صنعت فولاد به شمار می رود که 5 درصد از پوسته زمین را تشکیل می دهد. به دلیل اینکه ۹۸ درصد از سنگ آهن استخراج شده از معادن برای تولید فولاد مصرف می شود، جایگزین مناسبی برای آن در تولید فولاد وجود ندارد. برای فولاد سازی، سنگ آهن را تا دمای ۱۵۰۰ در کوره گداخته می شود و توسط تبدیل گر به فولاد تبدیل می شود.
برای اطلاعات بیشتر درباره سنگ آهن می توانید مقاله زیر را هم مطالعه کنید.
# حتما بخوانید
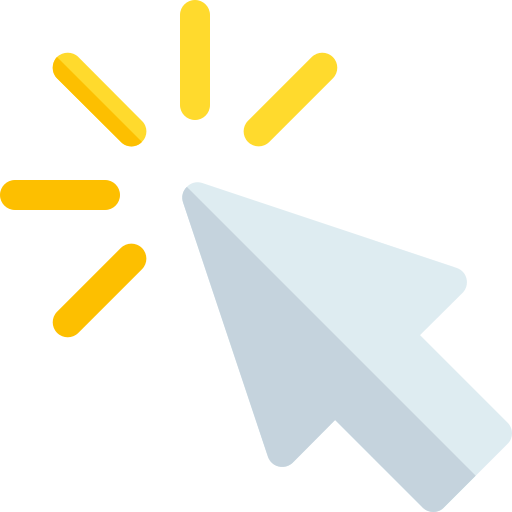
۲- زغال سنگ، سوخت تولید فولاد
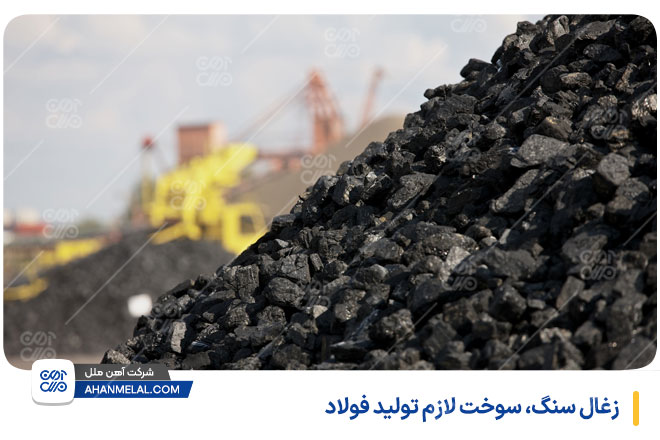
زغال سنگ یکی دیگر از مواد اولیه کارخانه فولاد است که به عنوان سوخت به کار می رود. در کوره بلند برای تولید فولاد ابتدا زغال سنگ باید حرارت داده شود و دمای کافی را برای گذاختن سنگ آهن فراهم سازد. توجه داشته باشید که زغال سنگ مستقیما برای گداختن سنگ آهن استفاده نمی شود زیرا زمانی که حرارت به آنها می رسد بسیار شکننده می شوند.
به همین منظور، زغال سنگ تا دمای ۱۴۰۰ درجه سانتی گراد در محیط بدون اکسیژن حرارت داده می شود و تبدیل به کُک شود. کُک تخلخل بالایی دارد (یعنی دارای حُفره های زیادی است) و باعث می شود تا اکسیژن از سنگ آهن آزاد شود و آهن خالص به دست آید.
۳- سنگ آهک، پاک کننده ناخاصی ها
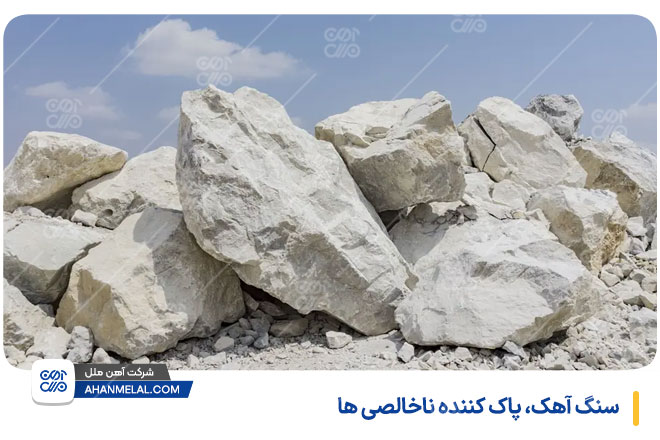
سنگ آهک یکی از مواد اولیه فولادی است و پاک کننده نا خالصی هایی همچون گوگرد، فسفر و سیلیسیم دی اکسید است. سنگ آهک با ناخالصی ها ترکیب می شود و سرباره ایجاد می کند. بعد سرباره از فولاد جدا شده و حذف می شود. این فرآیند باعث بهبود کیفیت فولاد می شود. همچنین آهک عمر مواد نسوز یا اصطلاحا مواد «دیرگداز» را بیشتر می کند.
۴- قراضه آهن، عامل خنک کننده
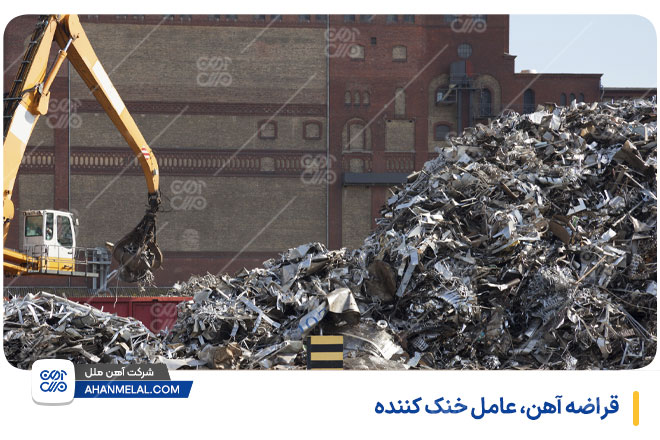
قراضه آهن یا ضایعات به معنی فولادی است که عمر مفید خود را به پایان رسانده است. ضایعات یا فولاد بازیافتی بعد از جمع آوری ابتدا وارد محیطی به نام «حوضچه های قراضه» می شود و در آنجا از اجسام اضافی مانند پلاستیک، چوب و غیره جداسازی می شود و آماده ذوب در کوره می شود. علاوه بر صرفه جویی در مصرف مواد اولیه فولاد، قراضه آهن به عنوان عامل خنک کننده در ذوب آهن کاربرد دارد.
در کشور ما نیز، کارخانه های بزرگی مانند شرکت فولاد مبارکه اصفهان از قراضه های آهن برای تولید فولاد استفاده می کنند. در کوره های قوس الکتریکی فولاد مبارکه اصفهان حداکثر از ۱۰ درصد آهن قراضه و ۹۰ درصد آهن اسفنجی استفاده می شود.
۵- گُندِلِه آهن: سرعت دهنده
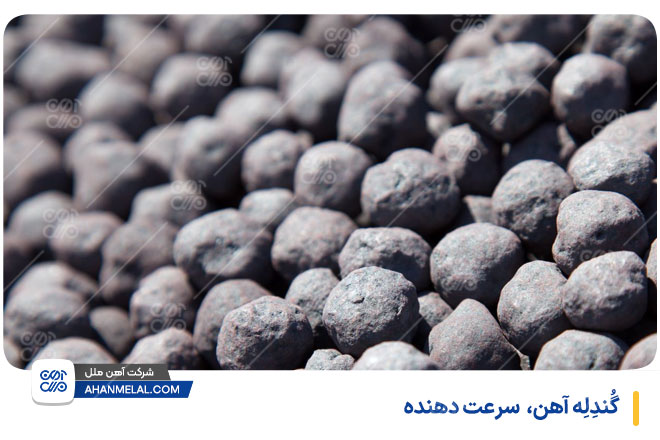
گُندِلِه آهن، گلوله کوچکی است که از سنگ آهن بهدست می آید. استفاده از گُندِلِه آهن به دلیل تخلخل بالا (دارای حفره های زیاد)، احیای آهن را سرعت می بخشد. در روش احیای مستقیم آهن، گازهای هیدرورکربنی در کوره آزاد می شود. آزاد شدن این گارها باعث می شود تا اکسیدهای آهن کاهش یافته و اصطلاحا «احیا» شود. در مقاله زیر می توانید اطلاعات بیشتری درباره این فرآورده بهدست آورید.
# حتما بخوانید
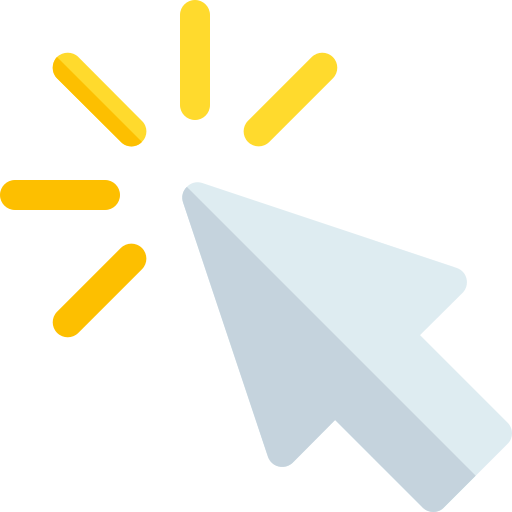
۶- آهن اسفنجی: کاهنده اکسید
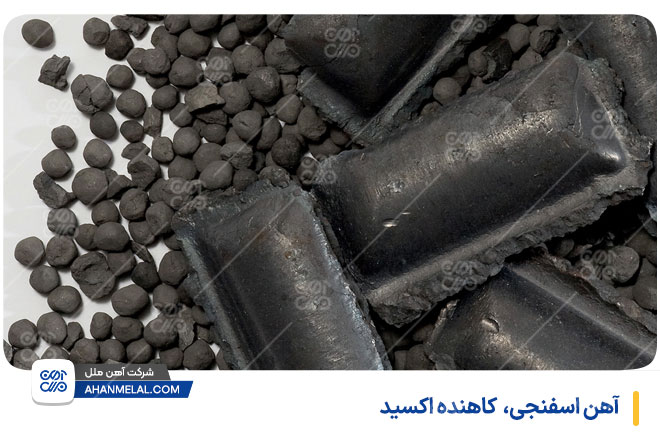
آهن اسفنجی یا آهن احیای مستقیم (DRI) یکی دیگر از مواد فولادسازی است که اکسیژن آن از طریق هیدروژن و کربن حذف شده است. مزیت استفاده از آهن اسفنجی، تولید فولاد با گریدهای بالا است. سازندگان فولاد با استفاده از آهن اسفنجی می توانند سنگ معدن های با عیار پایین تر و ضایعات آهنی کم تری استفاده کنند که در هزینه ها صرفه جوی می شود.
روش های تولید فولاد
دو روش رایج تولید فولاد، تولید فولاد به روش کوره بلند و تولید فولاد به روش کوره قوس الکتریکی انجام می شود. روش تولید فولاد با کوره بلند قدیمی تر است و هزینه بیشتری نسبت به کوره قوس الکتریک دارد. در ادامه این دو روش را توضیح می دهیم.
1- تولید فولاد به روش کوره بلند
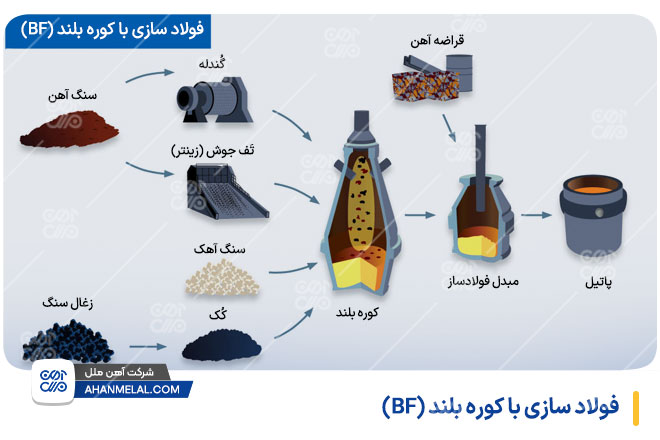
در فولاد سازی با کوره بلند، مواد اولیه فولادی مانند سنگ آهن، سنگ آهک، گندله و کُک را درون کوره بلند می ریزند. توجه داشته باشید که سنگ آهن بعد استخراج از معدن سریعا وارد کوره نمی شود و طی فرآیندی به نام «زینترینگ» یا «تَف جوشی» به ذرات کوچکتر تبدیل می شود. این ذرات اندازه مناسبی برای ذوب شدن در کوره دارند و فرآیند ذوب را سریع تر می کنند.
در تولید فولاد به روش کوره بلند از مواد اولیه فولادسازی از جمله سنگ آهن، زغال سنگ، سنگ آهک و فولاد بازیافتی استفاده می شود. در تولید فولاد به روش کوره بلند به طور متوسط ، ۱۳۷۰ کیلوگرم سنگ آهن، 780 کیلوگرم زغال سنگ متالورژی، ۲۷۰ کیلوگرم سنگ آهک و 125کیلوگرم فولاد بازیافتی برای تولید ۱ تُن فولاد خام مصرف می شود.
۲- تولید فولاد به روش کوره قوس الکتریکی
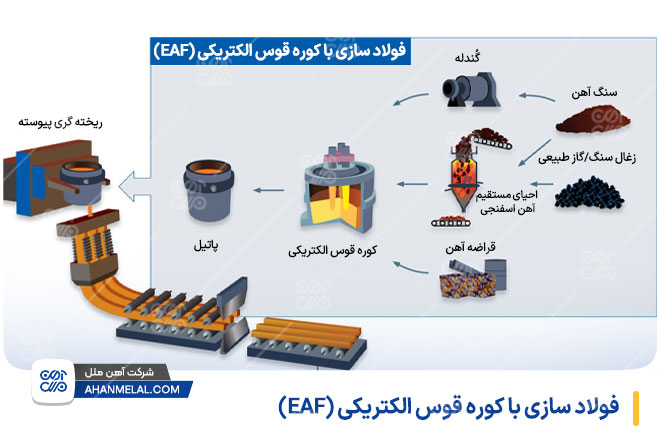
کوره قوسی الکتریکی (EAF) نوعی کوره است که استفاده از شار فلزی آهن و فولاد را سریعا ذوب می کند. در روش فولاد سازی با کوره قوس الکتریکی، ۳ الکترود گرافیتی برای ایجاد قوس الکتریکی به کار می رود. در واقع در این روش به جای استفاده از زغال سنگ برای تولید گرما از انرژی برق استفاده می شود. در روش تولید فولاد با کوره قوس الکتریکی دمای ذوب به ۱۸۰۰ درجه سانتی گراد هم می رسد.
در فولاد سازی با کوره قوس الکتریکی عمدتاً از فولادهای بازیافتی و آهن اسفنجی یا فلز داغ و برق استفاده می شود. در تولید فولاد به روش کوره قوس الکتریکی به طور متوسط، ۷۱۰ کیلوگرم فولاد بازیافتی، ۵۸۶ کیلوگرم سنگ آهن، ۱۵۰ کیلوگرم زغال سنگ، ۸۸ کیلوگرم سنگ آهک و ۲.۳ گیگا ژول اکتریسیته مصرف می شود.
برای تهیه فولاد از چه فلزی استفاده میشود؟
برای تهیه فولاد از فلز آهن استفاده می شود. آهن به صورت سنگ آهن در پوسته زمین وجود دارد و باید ناخالصی های آن را جدا (فرآوری) کرد. سپس آهن فرآوری شده به سمت کوره های ذوب می رود و آهن خالص بهدست می آید.
تامین مواد اولیه فولاد چگونه است؟
تأمین مواد اولیه فولاد از معادن بزرگ کشور انجام می شود. روند خرید این مواد تقریبا پیچیده است و نیاز به هماهنگی های دقیق با واحدهای تولیدی دارد. همچنین، یکی از چالش های پیش رو تأمین کنندگان، قیمت مواد اولیه فولادی است. درست است که ایران معادن بزرگ مواد اولیه فولاد سازی را در اختیار دارد ولی بخشی مواد لازم از منابع خارجی تأمین می شود.
کلام آخر
ممهم ترین مواد اولیه فولاد سازی شامل سنگ آهن، زغال سنگ، سنگ آهک، قراضه آهن، کُک و آهن اسفنجی می شود. روش های تولید فولاد به ۲ شکل رایج کوره بلند و کوره قوس الکتریکی است. تولید فولاد به روش کوره قوس الکتریکی به دلیل هزینه های پایین، ارزان تر از روش کوره بلند است.