۴ روش ریخته گری چدن
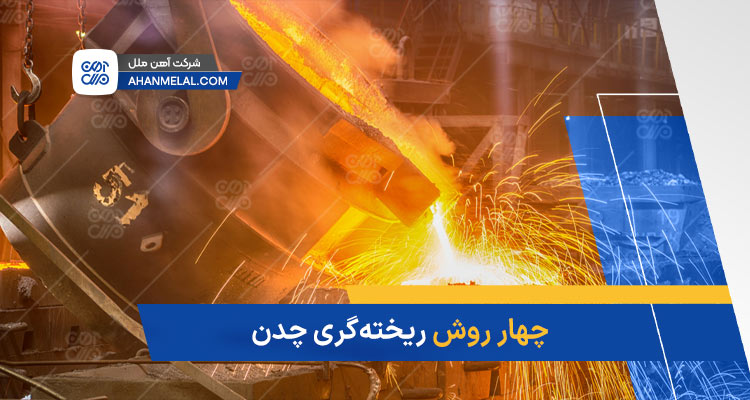
ریخته گری چدن برای تولید قطعات و اجزای ضروری در صنعت، نقش حیاتی دارد. در ریخته گری، آهن مذاب در قالبهای مخصوص ریخته شده و به اشکال مختلف و پیچیده تبدیل میشود. ریخته گری انواع چدن از چهار روش ۱- قالب ماسه ای، ۲- روش دقیق، ۳- لاست فوم و ۴- قالب دائمی قابل انجام است. هر کدام از این روشها که در ادامه بررسی میکنیم مزایا، معایب و روش کار مخصوص به خود را دارند که برای چدنهای متفاوت مناسب بوده و منجر به تولید قطعات با ویژگیهای متفاوت خواهند شد.

نسخه صوتی مقاله ۴ روش ریخته گری چدن
چدن چیست؟
چدن یک آلیاژ آهنی است که حدود ۲ تا ۴% کربن، حدود ۲% سیلیسیم و مقادیری از منگنز دارد، همچنین ردپایی از ناخالصیهایی مانند گوگرد و فسفر نیز در آن دیده میشود.
چدن با احیای سنگ آهن در کوره بلند تولید میشود. این محصول نسبت به اکثر فولادها مقاومت بالاتری در برابر خوردگی از خود نشان میدهد و قابلیت ریخته گری آسانی دارد، به همین دلیل از ریخته گری چدن برای ساخت قطعات و دامنه وسیعی از کاربردها استفاده میکنند.
# حتما بخوانید
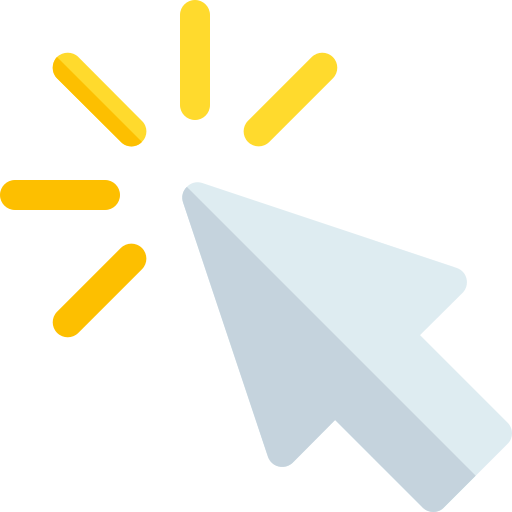
ریخته گری چدن چیست و چرا اهمیت دارد؟
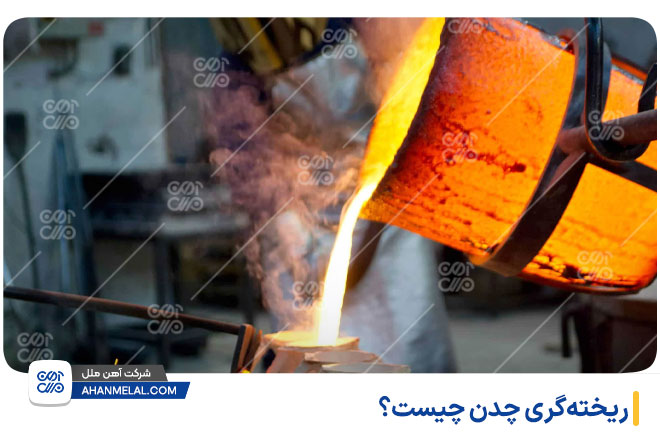
زمانی که از اصطلاح «ریخته گری چدن» صحبت میکنیم، منظور چدن ذوب شدهای است که در قالبها ریخته میشود تا محصولات و قطعاتی با اندازه و شکلهای متنوع ساخته شوند.
به طور کل خدمات ریخته گری چدن یکی از روشهای تولید قطعات و یا تولید قسمتی از محصولات مختلف است.
در ریختهگری، فلزات و آلیاژها به صورت مذاب در قالب ریخته میشوند تا پس از انجماد، شکل فضای خالی قالب را به خود بگیرند. در نهایت قطعهای جامد با شکل، ابعاد و خواص مورد نظر، از درون قالب خارج میشود.
جالب است بدانید برای آن دسته از مواد آلیاژی که شکننده هستند و انعطاف پذیری کمی دارند (مانند چدن معمولی)، فرایند ریختهگری تنها فرآیندی است که می توان برای شکل دادن به آنها استفاده کرد.
انواع روش های ریخته گری چدن (۴ روش)
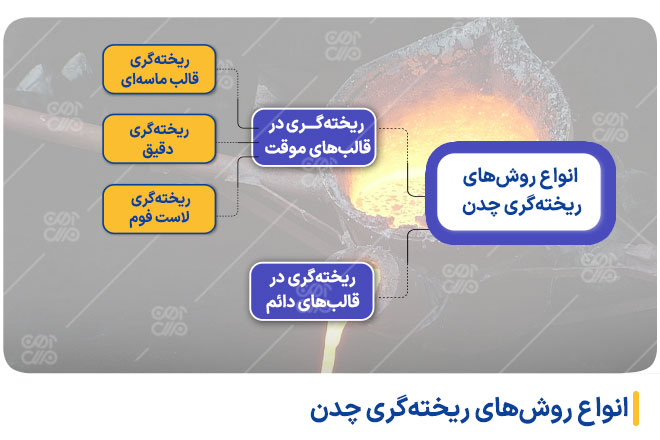
روشهای مختلفی برای ریخته گری چدن ها استفاده میشود. انتخاب روش ریخته گری بر اساس نوع چدن و نوع محصولی که قرار است ساخته شود، انجام میشود. اگر بخواهیم این روشها را از نظر قالب های ریخته گری چدن دسهبندی کنیم به دو دسته بر میخوریم:
۱- ریخته گری در قالبهای موقت (که سه روش مختلف دارند)
- ریخته گری قالب ماسهای (ماسه تر، ماسه CO2، ماسه فوران (چسب سرد))
- ریخته گری دقیق
- ریخته گری لاست فوم
۲- ریخته گری در قالب دائم (یک روش دارد)
کدام روش ریختهگری چدن در ایران محبوبتر است؟
در میان روشهایی که بالا گفتیم، انواع کارگاه ریخته گری چدن بیشتر از ۲ روش «قالب ماسه ای» و «لاست فوم» استفاده میکنند. و درنهایت نیز محبوبترین روش ریخته گری چدن در ایران را باید روش ریخته گری چدن در قالب های ماسه ای نام برد.
بیایید در ادامه با این روشها بیشتر آشنا شویم.
۱- ریخته گری چدن با قالب ماسهای (Sand Casting)
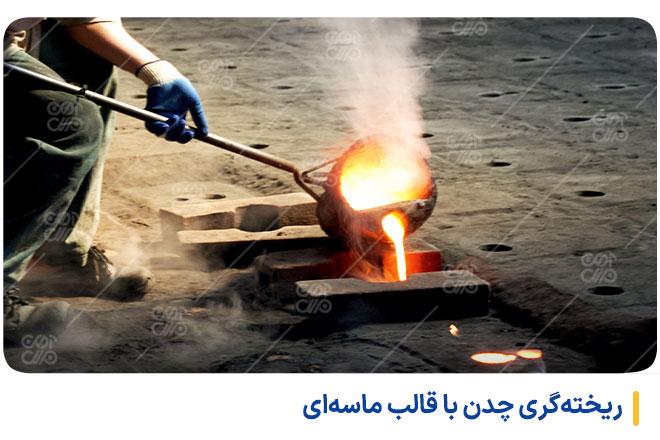
ریخته گری با قالب ماسهای فرایندی کم هزینه و چندمنظوره با قدمت بالاست، که کاربرد زیادی در صنعت متالورژی و تولید فلز دارد. در این روش قالب ریخته گری چدن از جنس ماسه است.
ماسه ریخته گری چدن نیز می تواند ماسه تر، ماسه CO2، ماسه فوران باشد، اما معمولا ماسه CO2 (یک نوع ماسه ریخته گری که با اضافه کردن گاز CO2 فراوری میشود) است.
استفاده از ریخته گری ماسه ای در تولید قطعات چدنی و فلزی محبوبیت زیادی دارد، زیرا ماسهها در برابر آتش و گرما مقاوم بوده و به اصطلاح نسوز هستند. این روش بدون نیاز به ماشینها و دستگاههای پیشرفته میتواند تولیدات انبوه با هزینههای پایین به بازار عرضه کند.
روش کار ریخته گری چدن با قالب ماسه ای
برای ایجاد قالب در این روش، از جعبهای ماسهای استفاده میکنند. مدل مورد نیاز برای ساخت قطعه نیز که از قبل تهیه شده داخل قالب ماسهای قرار داده میشود.
با توجه به نوع ماسه، چسب یا رطوبتِ موجود در آن، باعث فشرده شدن ماسهی اطراف مدل شده و طرح آن درون ماسه شکل میگیرد.
بعد از شکلگیری طرح، مدل را از ماسه خارج میکنند. سپس فضای ایجاد شده را با مواد مذاب پر کرده یا اصطلاحا ریخته گری انجام میشود.
برای ریخته گری از شبکه راهگاهی (Gating System) استفاده میشود که وظیفه رساندن مواد مذاب به قطعه را بر عهده دارد.
کاربرد ریخته گری چدن با قالب ماسه ای
ریخته گری قطعات چدن به روش ماسه ای، به دلیل تنوع در تولید قطعات با ابعاد مختلف، انتخاب اول بسیاری از کارخانههای متالورژی است. این روش امکان تولید انبوه قطعات متنوع را با هزینهای مقرونبهصرفه فراهم میکند. از جمله قطعات چدنی که به روش ریخته گری ماسه ای تولید میشوند میتوان به این موارد اشاره کرد:
- پیستون کمپرسور
- دمنده و پروانه
- بوش
- میل بادامک
- کبابپز و مشعل
- تجهیزات قالببندی
- تجهیزات الکترونیکی
- تابه تخلیه روغن موتور
- قطعات خودروسازی
- قطعات ماشینآلات معدن
- اتصالات
مزایای ریخته گری چدن با قالب ماسه ای
قدمت بالای این روش ریخته گری، نشان دهنده مزایای بالای آن است که مهمترین آنها عبارتند از:
- امکان ساخت قطعات پیچیده
- انعطافپذیری در طراحی، اندازهها و اشکال
- مقرون به صرفه بودن و صرفهجویی در هزینهها
- تولید سریع
- ایدهآل برای تولیدات کوتاه مدت
معایب ریخته گری چدن با قالب ماسه ای
با اینکه ریخته گری ماسه ای گزینه اول در ریخته گری چدن است، اما نمیتوان از عیوب این روش که در ادامه اشاره میکنیم، چشمپوشی کرد:
- دقت ابعادی پایینتر نسبت به سایر فرایندها
- وابستگی کیفیت به اجرای صحیح فرایند
- استحکام کمتر به دلیل تخلیل زیاد
- تولید قطعات با سطح نسبتا خشن
۲- ریخته گری چدن به روش ریخته گری دقیق (Investment Casting)
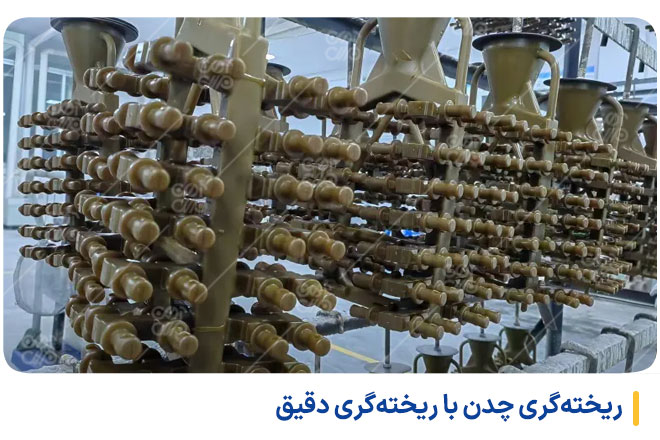
به ریخته گری دقیق، ریخته گری مومی نیز گفته میشود. این روش ریخته گری معمولاً برای تولید قطعات پیچیده که دیوارههای نازک دارند، استفاده میشود. در ریخته گری چدن نشکن داکتیل و ریخته گری چدن خاکستری از این روش زیاد استفاده میشود.
این روش قادر به ساخت قطعاتی با ضخامت دیوار ۰٫۶ میلیمتر تا ۷٫۵ سانتیمتر بوده و میتوان آن را در دو مدل انجام داد: روش مستقیم (مدل موم اصلی) و روش غیر مستقیم (نیازی به استفاده از موم نیست).
روش کار ریخته گری چدن با ریخته گری دقیق
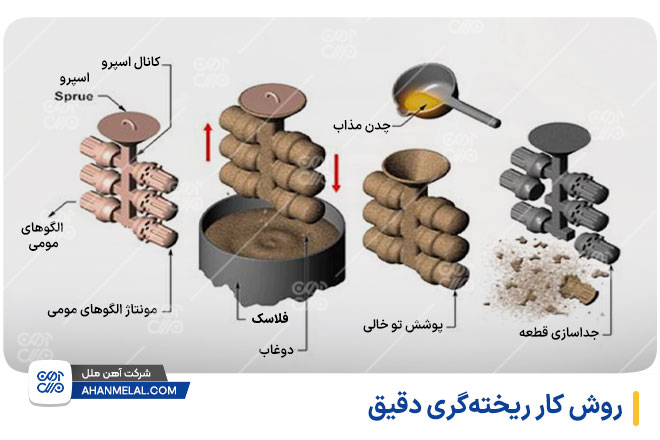
ابتدا یک الگوی اصلی با استفاده از موم، خاک رس، چوب و … توسط متخصص قالبساز ساخته میشود.
سپس قالب اصلی را با ریختهگری یا ماشینکاری میسازند. این قالب باید منطبق با الگوی اصلی و جنس آن (که در مرحله قبل ساخته شد) باشد.
در مرحله بعد، الگوهای مومی (البته میتوانند از پلاستیک یا جیوه منجمد نیز باشند) با استفاده از قالب اصلی ساخته میشوند. یعنی الگوهای مومی با تزریق یا ریختن موم مذاب به قالب اصلی و سپس سفت شدن آن ساخته میشوند.
اکنون مرحله مونتاژ الگوهای مومی است. الگوهای موم روی یک اسپرو (sprue) موم معمولی مونتاژ میشوند. با این کار مواد مذاب میتوانند از طریق کانال اسپرو، پس از حذف موم، به قالب برسد.
در ادامه، الگوی مونتاژ شده، به روش غوطهوری پوششدهی میشود. یعنی الگو را در دوغابی از مواد نسوز غوطه ور میکنند تا سطحی یکنواخت به نام «پرایم کت» ایجاد شود.
بعد از خشک شدن الگو، حذف موم الگو از قالب با فرآیند ذوب و تبخیر انجام میشود. مومزدایی یکی از دلایل اصلی ترک خودن پوسته است. (ترک پوسته رایجترین عیب ریختهگری دقیق است.)
در مرحله بعد قالب پیشگرم میشود، سپس فلز مذاب را در قالب توخالی ریخته و به آن اجازه خنک شدن میدهند.
مرحله آخر نیز جداسازی و پردازش قطعه است.
کاربرد ریخته گری چدن با ریخته گری دقیق
به دلیل مزایای خاص این روش، از ریخته گری دقیق بیشتر برای صنایع و تجهیزات نظامی، تجهیزات هوافضا، پزشکی، داندانپزشکی و … استفاده میشود.
مزایای ریخته گری چدن با ریخته گری دقیق
همانطور که از نام این روش مشخص است، تولید قطعات به روش ریخته گری دقیق، ظرافت و مزیتهای زیادی به همراه خواهد داشت از جمله:
- قابلیت تولید قطعات ظریف
- کیفیت سطح فوقالعاده
- دقت ابعادی بالا
- قابلیت تولید قطعلات با پیچیدگی بالا
- بدون ایجاد خط جدایش یا رگه مذاب
معایب ریخته گری چدن با ریخته گری دقیق
محدودیتها و عیوب ریخته گری چدن در روش ریخته گری دقیق عبارتند از:
- هزینه بالای ساخت الگو و قالب
- هزینه بالای نیروی کار
- محدودیت در اندازۀ قطعات قابل ساخت (معمولا از ۳ گرم تا ۵ کیلوگرم)
۳- ریخته گری چدن به روش لاست فوم (Lost-foam casting)
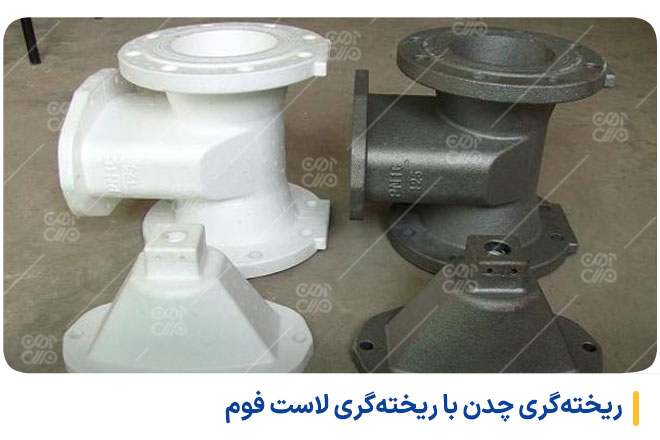
لاست فوم به معنای فوم فداشونده است. این روش نسبت به روش ماسه ای پیشرفتهتر و جدیدتر است. روش لاست فوم در ریخته گری چدن خاکستری و ریخته گری چدن داکتیل (چدن نشکن) کاربرد بیشتری دارد.
قالب ریخته گری چدن در این روش، فوم یک بار مصرف (مدل تبخیرشونده) است، به همین دلیل به آن ریخته گری فومِ فداشونده میگویند.
ریخته گری لاست فوم چدن بسیار شبیه به روش ریخته گری دقیق است، فقط در آن به جای «موم» از «فوم» استفاده میشود. در نتیجه برتری این روش حذف مرحله ذوب و خارج کردم موم از قالب است، زیرا فوم در مراحل ریختهگری خود به خود تبخیر خواهد شد.
روش کار ریخته گری چدن به روش لاست فوم
قالب لاست فوم معمولا قالب فلزی یا قالب آلومینیومی تراش خورده است. الگوی فوم نیز از جنس پلی استایرن، در قالب ساخته میشود.
روند ساخت الگو، دقت بسیار زیادی نیاز دارد، زیرا کیفیت و قابلیت اطمینانِ محصول نهایی در این مرحله تعیین میشود.
پس از ساخت الگو آن را با یک پوشش نسوز با قابلیت نفوپذیری میپوشانند و در شرایط بسیار کنترل شده خشک میکنند.
الگوی خشک شده در یک جریان از شن و ماسه قرار داده میشود، تا در شن الگویی را از خود به جا بگذارد.
در این مرحله فلز مذاب درون قالب ریخته میشود، با ریختن فلز مذاب، الگوی ساخته شده در مرحله اول بلافاصله بخار شده و از بین میرود. ریختن تا زمان پر شدن قالب ادامه خواهد داشت.
پس از پر شدن قالب و سپس منجمد شدن آن، قالب شنی شکسته میشود.
در مرحله آخر محصول نهایی در صورت لزوم تحت عملیات حرارتی یا عملیات اصلاحی قرار میگیرد.
نکته: در مرحله قالبشکنی، رایزر و سیستم وردی برداشته میشود تا برای تولید بعدی مجددا استفاده شود. بیشتر تجهیزات ریختهگری لاست فوم معمولا ۳ تا ۴ بار مورد استفاده قرار میگیرند. و از این رو تا حدودی با ابزارهای قالبگیری دائم مقایسه میشوند.
کاربرد ریخته گری چدن به روش لاست فوم
این روش برای ریخته گری قطعات با وزن ۰.۵ تا ۵۰ کیلوگرم مناسب است و برای قطعات بزرگتر ریخته گری ماسه ای پیشنهاد میشود.همچنین برای تولید قطعات فلزی با دقت بالا و پیچیدگی زیاد محبوبیت دارد. از این رو از ریخته گری لاست فوم عمدتا برای موارد زیر استفاده میکنند:
- قطعات سبک وزن
- تجهیزات راه آهن
- ماشینآلات کشاورزی
- تجهیزات میدان نفتی
مزایای ریخته گری چدن به روش لاست فوم
ریخته گری لاست فوم روشی نسبتا جدید است و مزایای آن تقریبا ترکیبی از مزیتهای ریخته گری ماسه ای و ریخته گری دقیق و به صورت زیر است.
- امکان تولید قطعات پیچیده
- قابل استفاده برای ریخته گریهایی که به ماهیچه نیاز دارند
- قالب خط شکاف ندارد (نیازی به زاویه خروج از قالب ندارد)
- عدم تشکیل پلیسه و کاهش نیاز به پرداخت قطعه و عملیاتهای نهایی
- کاهش هزینه تمام شده به دلیل کاهش هدر رفت مواد و کاهش ضایعات
- مراحل ساختِ کمتر نسبت به ریخته گری دقیق
- سهولت و انعطافپذیری در طراحی
- امکان ترکیب قطعات
- با صرفهتر و ارزانتر از روش ریخته گری دقیق
معایب ریخته گری چدن به روش لاست فوم
موارد زیر را میتوان به عنوان عیوب ریخته گری چدن به روش لاست فوم معرفی کرد:
- بالا بودن هزینه الگوسازی، مخصوصا در تیراژ بالا
- مقاومت پایین الگو و امکان آسیب دیدن آن
- امکان تخلخل در ریختهگری به دلیل فوم پلی استایرین سوخته
- امکان کم شدن یکپارچگی و کیفیت ساختاری قطعه
۴- ریخته گری چدن با قالب دائم
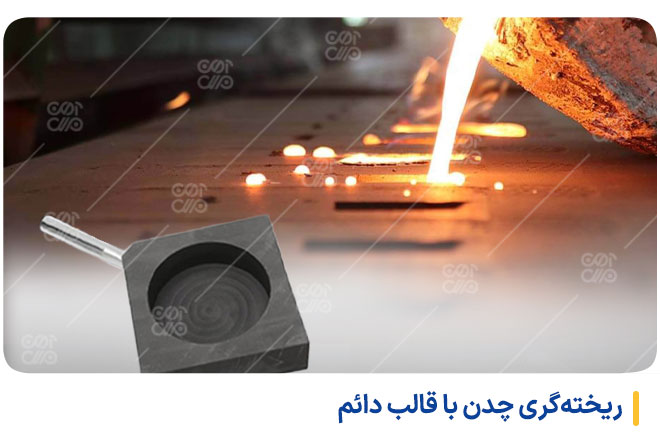
در کلیه روشهای ریخته گری انواع چدن ها که تا اینجا بررسی کردیم، قالب تماما از بین رونده بود. یعنی برای هر فرایند ریختهگری، قالب از بین میرفت و لازم بود برای ریختهگری بعدی دوباره قالبی جدید و نو آماده شود (فقط در روش لاست فوم، قالب چندبار قابل استفاده بود و بعد از بین میرفت).
اما در ریخته گری با قالب دائم از قالبهای دائمی (قالبهایی با عمر طولانی) استفاده میشود. عمر قالبها در این روش میتواند بین ۱۰۰ تا ۲۵۰۰۰ بار ریختهگری و یا حتی بیشتر باشد. ریخته گری قالب دائم برای تولید قطعات در تعداد زیاد و ضخامت دیواره نسبتا یکنواخت مناسب هستند.
اکثر قالبها در این روش از جنس فلز هستند، اما برای ریخته گری چدن از قالب با جنس گرافیت استفاده میشود. همچنین بیشتر چدن خاکستری به این روش ریخته گری میشود.
روش کار ریخته گری چدن با قالب دائم
نحوه ریخته گری چدن در قالبهای دائم به سه مدل متفاوت انجام میشود که در این بین ریخته گری تقلی (ریژه) کاربرد و محبوبیت بیشتری دارد.
۱- روش ثقلی (ریژه)
سادهترین قالبهای دائمی، انواع مختلف قالبهای ثقلی یا ریژه هستند. قطعات ساخته شده با قالبهای ثقلی در مقایسه با قطعات ریخته شده در روش ماسهای، کیفیت سطح، تلرانس ابعاد، دید ظاهری و خواص مختلف مکانیکی بهتری دارند.
در این روش، مواد مذاب بر اساس وزنی که دارند قالب را پر میکنند.
۲- روش تحت فشار
در این روش، مذاب تحت فشار معین محفظه قالب را پر میکند و انجماد نیز تحت فشار انجام میشود. در این روش امکان تولید قطعات پیچیدهتر وجود دارد. همچنین نسبت به روش ثقلی شرایط بهتری در خواص مکانیکی و همچنین رفع عیوب ریخته گری چدن به ایجاد حفره، به وجود میآورد.
۳- روش گریز از مرکز
در این روش، قالب تحت تاثیر نیروی گریز از مرکز پر میشود. دو نوع گریز از مرکز افقی و گریز از مرکز عمودی وجود دارد. به طور مثال روش گریز از مرکز افقی برای ریخته گری چدن نشکن و ریخته گری چدن خاکستری در تولید لوله با ضخامت کم استفاده میشود.
کاربرد ریخته گری چدن با قالب دائم
با این روش امکان ساخت قطعات معمولی و پیچیده از چرخدنده گرفته تا قطعات صنایع موتورسازی و فولادسازی فراهم است. از جمله این قطعات عبارتند از:
- پیستون موتور خودرو
- پوستههای جعبه دنده
- سرسیلندر
- چرخ دنده
- هزار خار
- جعبهدنده
- وسایل و اتصالات لولهکشی
- محفظه تزریق سوخت
مزایای ریخته گری چدن با قالب دائم
مزایای ریخته گری چدن با روش قالب دائمی را اینگونه میتوان بیان کرد:
- سرعت بالای تولید
- دقت ابعادی بالا
- قابلیت تکرار تولید قطعات یکنواخت
- عیوب ریختهگری کم
- کیفیت بالای سطح قطعه
- خواص فیزیکی و مکانیکی بالا
معایب ریخته گری چدن با قالب دائم
معیاب این روش به اندازه مزایای آن اهمیت داشته و منجر به عدم استفاده از این روش در ساخت بسیاری از قطعات میشود.
- عدم امکان تولید قطعه با همه آلیاژها
- لزوم استفاده از پوشش قالب
- غیراقتصادی بودن در تعداد کم
- عدم امکان تولید قطعات با اشکال خاص
- عدم امکان تولید قطعات بزرگ و سنگین
سخن آخر
فرایند ریخته گری چدن برای تولید قطعات مختلف از اشکال ساده تا اشکال پیچیده استفاده میشود. از ۴ روش ریخته گری چدن که در این مقاله بررسی کردیم، ۳ روش آن (قالب ماسه ای، لاست فوم، روش دقیق) از نوع قالب موقت بودند و روش چهارم از نوع قالب دائم است. با این چهار روش میتوان انواع چدن ریخته گری مانند چرخ دنده، شیر فلکه، بدنههای پمپ، میل لنگ، غلتک، تجهیزات فرایند شیمیایی، صفحه کلاچ، قالبهای شیشه، بوتههای ذوب فلز و … را تولید کرد.