انواع کوره در تولید آهن آلات
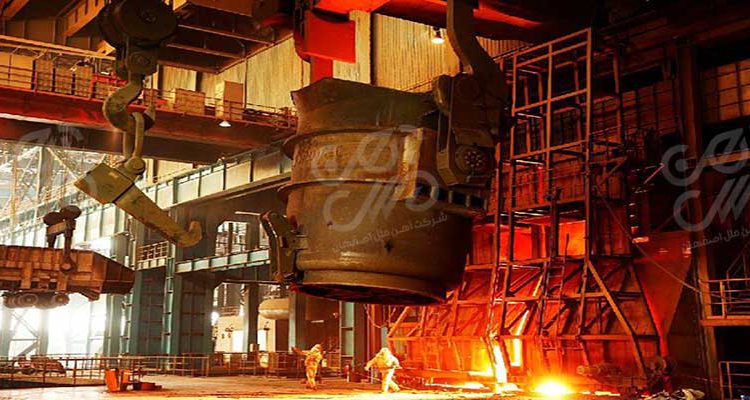
فرآیند اصلی تولید آهن آلات مدرن، استفاده از انواع کوره است. این کوره ها تعیین کننده ی خصوصیات مواد و کیفیت محصول نهایی میباشد.
در بازار، طی فرآیند تولید به عرضه کالاهای با کیفیت به عملیات گرمایشی و سرمایشی اعمال شده وابسته میباشد. بنابراین با آهن ملل همراه باشید.
انواع کوره هریک در مراحل مختلف کاربرد دارد که این مراحل شامل:
- پیش گرمایش میله
- تولید محصولات آهنی و غیرآهنی مثل ذوب قراضه
- شکل دهی گرم صفحات فلزی
- عملیات حرارتی فولاد
در این مقاله به بررسی اختصاصی انواع کوره و مزایا و معایب هریک میپردازیم.
انواع کوره ها
کوره ها انواع متفاوتی در زمینه ی تولید آهن آلات دارد که شامل:
- کوره بوته ای
- کوره القایی
- کوره کوپلا
- کوره مقاومتی الکتریکی
- کوره قوس الکتریکی
- کوره شعله ای
کوره بوته ای
کوره بوته ای یکی از قدیمی و ساده ترین انواع کوره ها میباشد که در واحد ریخته گری مورد استفاده قرار میگیرد.
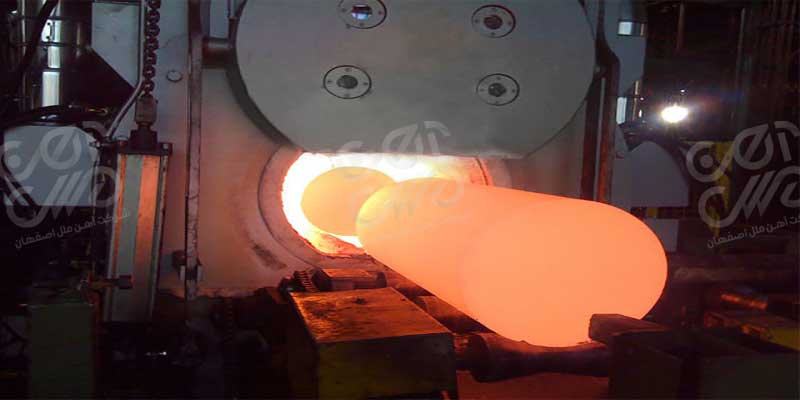
توجه به کوره بوته ای در گذشت زمان و پیشرفت تکنولوژی کمتر شده اما در شرایط خاص همچنان کوره بوته ای مورد استفاده قرار میگیرد.
در کوره بوته ای مواد اولیه و سوخت باهم تماسی ندارند و مواد درون کوره با استفاده از حرارت به مواد مذاب تبدیل میشود.
انواع کوره بوته ای کاربردهای متفاوتی دارند زیرا مواد نسوز مختلفی در ساخت آن به کار میرود.
رایج ترین بوته ها شامل بوته گرافیتی، سیلیکون کاربایدی، شاموتی میباشند.
از بوته فولادی برای ذوب آلیاژهای با نقطه ذوب پایین و آلیاژهایی مثل منیزیم که میل ترکیبی زیادی با اکسیژن دارند، استفاده میشود.
سوخت کوره بوته ای با مصرف گازوئیل، مازوت، گاز طبیعی و الکتریسیته تامین میشود.
انواع کوره بوته ای برحسب نوع ساختمان به صورت کوره ثابت، کوره ثابت با بوته متحرک یا گردان ساخته میشود.
مزایا و معایب کوره بوته ای
کوره بوته ای مزایایی دارد که سبب گردیده استفاده از آن در کارگاه های کوچک در اولویت باشد که این مزایا شامل:
- سادگی و سهولت ساخت
- ارزانی و مقرون به صرفه بودن این کوره
- کیفیت مذاب خوب
از عیب این کوره میتوان گفت که تلفات حرارتی در این کوره ها بالا میباشد.
کوره القایی
این نوع از کوره جزو کوره های مدرن محسوب میشود.
در اثر عبور جریان الکتریکی میدان مغناطیسی در سیم پیچ ایجاد میشود که سبب به وجود آمدن جریان های گردابی در فلز میشود که باعث ذوب شدن آن میشود.
کوره القایی بر حسب فرکانس به ۳ دسته تقسیم میشود:
- فرکانس پایین ۵۰ هرتز
- فرکانس متوسط ۲۰۰ تا ۱۰۰۰۰ هرتز
- فرکانس ۱۰۰۰۰ هرتز به بالا
کوره های فرکانس پایین، راندمان پایینی دارند که بیشتر به عنوان کوره های نگهدارنده مورد استفاده قرار میگیرد همچنین این نوع از کوره ها ب ای ذوب توصیه نمیشوند.
کوره های فرکانس بالا برای ذوب در آزمایشگاه ها مورد استفاده قرار میگیرند.
مزایا و معایب کوره القایی
مزایای کوره های القایی شامل:
- توزیع حرارت مطلوب
- مصرف انرژی کمتر نسبت به کوره مقاومتی
- کنترل ترکیب شیمیایی
- عدم محدودیت افزایش دما
عیب این کوره از جمله استفاده از الکتریسیته باعث افزایش هزینه میشود.
به دلیل وجود تلاطم و سرد بودن مذاب در سطح فوقانی امکان تصفیه مذاب وجود ندارد به همین دلیل از قبل باید تمیز شود.
کوره کوپلا
استفاده از کوره کوپلا، متداول ترین روش ذوب چدن میباشد.
ساختمان کوره کوپلا استوانه ای فولادی میباشد که با جداره نسوز پوشیده شده استکه قطر این ساختمان متناسب با ظرفیت و سرعت ذوب متغیر میباشد.
بخش های جانبی این کوره شامل پیش گرم کن هوا، ریل شارژ و محل تصفیه گازهی خروجی میباشد.
این کوره در تماس مستقیم با شارژ ظرفیت ذوب از ۱۰۰ تا ده ها تن دارد. براساس نحوه و نوع مصرف سوخت انواع کوره در صنعت استفاده میشود.
مزایا و معایب کوره کوپلا
با استفاده از کوره کوپلا میتوان حجم مذاب بالایی آماده کرد همچنین نحوه کار با این کوره ساده میباشد.
کوره های کوپلا انعطاف پذیری کمی در رسیدن به فوق گدازهای بالا دارند.
کوره مقاومتی الکتریکی
در این نوع از کوره حرارت لازم برای ذوب شارژ از طریق عبور جریان الکتریکی از المنتها تامین میشود.
از کوره های مقاومتی برای عملیات حرارتی، پیش گرم کردن برای شکل دهی با فشار و ذوب فلزات استفاده میشود.
ساخت المنت ها از آلیاژ هایی با نقطه ذوب بالا و مقاوم به خوردگی و اکسیداسیون میباشد.
انواع کوره مقاومتی در دو نوع
- کوره مقاومتی با گرم کننده مستقیم
در این کوره جریان برق با ولتاژ گرم عبور میکند و جریان شارژ از خود شارژ عبور میکند. همچنین این کوره برای گرم نگه داشتن و ذوب کاربرد دارد.
- کوره مقاومتی با گرم کننده غیرمستقیم
در این کوره جریان برق از المنت های فنری که دور کوره پیچیده شده میگذرد و حرارت در ابتدا به کوره و از آنجا به بوته شارژ منتقل میشود.
مزایا و معایب کوره مقاومتی الکتریکی
در این روش ترکیب شیمیایی مذاب کنترل میشود.
عیب این کوره علاوه بر بالا بودن هزینه ها به دلیل استفاده از الکتریسیته، ظرفیت این کوره ها حداکثر ۵۰۰ کیلوگرم میباشد که این ظرفیت کم است.
کوره قوس الکتریکی
ساختمان کوره قوس الکتریکی یک حمام بزرگ با بدنه فولادی پوشیده شده با ماده نسوز میباشد.
سقف و بدنه ای این کوره با لوله های آبگرد پوشیده شده است چون دمای بدنه بالا میباشد که باعث از بین رفتن ماده نسوز شود.
قوس الکتریکی نیز در دو نوع میباشد که شامل:
- قوس الکتریکی مستقیم
قوس الکتریکی مستقیم در ذوب فولاد و چدن استفاده میشود.
- قوس الکتریکی غیر مستقیم
قوس الکتریکی غیر مستقیم برای ذوب آلیاژهای مس مورد استفاده قرار میگیرد.
مزایا و معایب کوره قوس الکتریکی
از قراضه های ارزان میتوان در این کوره استفاده کرد.
تمیز بودن کوره قوسی الزامی نیست.
در این کوره دمای قوس ایجاد شده بیشتر از کوره القایی میباشد.
در کوره القایی هزینه انرژی در مقایسه با کوره قوس کمتر است.
هزینه گرافیت و نسوز مورد استفاده در کوره قوس باعث افزایش هزینه های عملیاتی میشود.
کوره شعله ای
در قرون وسطی از کوره شعله ای برای ذوب برنز به منظور ریخته گری زنگ های کلیسا استفاده میشود.
در این کوره مواد شارژ در تماس مستقیم با محصولات احتراق قرار میگیرد و ذوب میشود.
شارژ داخل کوره به دو طریق : درب و سقف کوره انجام میشود.
سوخت مصرفی برای کوره شعله ای، گازوئیل یا گاز طبیعی میباشد.
ظرفیت کوره شعله ای برای ذوب آلیاژهای غیرآهنی، ۱۵ تا ۷۵ تن متغیر میباشد اما کوره های ۵۰۰ کیلوگرمی نیز ساخته شده است.
این کوره های شعله ای تا ۹۰ تن ظرفیت دارند. ساخت انواع کوره شعله ای به شکل مکعب مستطیل و استوانه ای میباشد.
مزایا و معایب کوره شعله ای
کوره ی شعله ای دارای مزایایی میباشد که شامل:
- ساخت کوره ی شعله ای ساده است.
- حجم و سرعت بالایی در ذوب دارد.
- احتیاج به سرمایه گذاری زیادی ندارد.
عیب کوره شعله ای، راندمان کوره ها پایین است چون درجه حرارت مذاب بالا نمیباشد.